It all started back in 1962 with fish at FRoSTA. At that time, material flow control was done exclusively on paper, and until 1970 the frozen food expert from Bremerhaven even had its own fishing fleet. Nowadays, the company relies on digitalisation in almost every area – without its own vessels, but with visible success.
A little spoiler: neither Ben Windhorst, IT Director and Digital Transformation Officer at FRoSTA, nor Heliodor Rawski, Head of SCM Logistics at FRoSTA, could fully “capture” in concrete figures how much IT actually goes into their fish in their interview with LOGISTICS PILOT today. Nevertheless, one thing is clear for Windhorst: “A lot of IT goes into fish – and this is increasing, since our transformation process is far from complete.” The company took its first steps toward digitalisation back in the 1980s, when it began to map an increasing number of business processes via software systems. This development has included full automation of the warehouse management software since the early 2000s and a fully integrated transport planning system since 2018.
Nowadays, digitalisation at FRoSTA is becoming particularly visible in areas involving the end consumer, as well as in supply chain processes and in the networking of internal staff members. For example, blockchain technology allows the company to securely transmit more information to its customers whilst, at the same time, supporting the FRoSTA vision of greater transparency and sustainability. This includes tracking important product data – not only for fish, but also for ready meals, vegetables, fruits and herbs. “The ingredient tracker on our website allows all ingredients and countries of origin of our products to be tracked throughout the supply chain, i.e. where they come from, how they are processed and how large their CO2 footprint is,” cited Windhorst as an example.
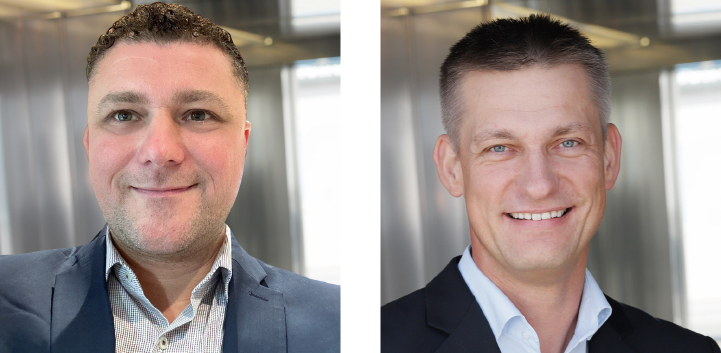
„Es geht nicht ohne die Beteiligung des Menschen“
Both Windhorst and Rawski regard the approx. 1,800 FRoSTA employees as crucial in the digitalisation journey. Windhorst also likes to think of this journey as a relay race, in which the baton pass – and therefore the IT interfaces – are particularly important. “Despite all the automation, this would not be possible without human input,” stressed Rawski. That is why the FRoSTA IT team has migrated all the workflows of various divisions, departments and branches to Microsoft Azure over the past three years. Moreover, new cloud solutions were implemented during the COVID-19 crisis, meaning that FRoSTA is now able to allow its employees to work completely from home without causing any constraints on quality. However, both IT experts are already busy thinking up new services, new solutions and new benefits. “We are currently working on a way to integrate suppliers, customers and employees into the FRoSTA world even further. We also have digital delivery notes on our agenda for the near future,” Rawski added.
Reflecting on the past three years, the frozen food product manufacturer weighs up both the ups and downs: “On the one hand, during the pandemic, when many restaurants had to shut their doors and people had a taste for delicious ready meals, we were able to attract a large number of new customers who have since stayed with us,” Windhorst stated. “Since our product range extends to large areas of the food service industry, for example in schools and department stores, we also had to accept significant cuts when these areas were also restricted to limited operations due to COVID-19,” he added. In the fish segment, fish fingers sold particularly well during the COVID-19 pandemic. They are amongst the classics of the most popular lunch items, especially for children, the company reports. (bre)
Facts
FRoSTA AG
Product portfolio: Fish; fish-, meat- and vegetable-based ready meals; vegetables; fruits; and herbs
Employees: 1.800
Headquarters: Bremerhaven
2021 Turnover: EUR 527 million